*This article was published in Vol. 51 No. 6 of Cycle Canada digital magazine.
Common sense tells us all that speeds up must at some point slow down. Oddly enough, despite this, we spend a disproportionate amount of our time focusing on acceleration without worrying too much about the flip side of the coin. However, in the real world, it is more often the deceleration aspect that matters most, so much so that our lives can sometimes depend on it. This month, we will therefore devote our column to deepening our knowledge of the braking system.
Kinetic to thermal
It goes without saying that the purpose of a vehicle’s braking system is to slow down and stop the vehicle. Theoretically speaking, however, one could rightfully claim that its purpose is to convert kinetic energy into thermal energy. One of the underlying laws of physics is that energy can neither be created nor destroyed, it can only change forms. In the case of a vehicle’s braking system, the brakes transform the vehicle’s kinetic energy into heat (as anyone who has attempted to touch a brake rotor immediately after a stop can attest). So, let’s now see how this is accomplished.
The drum
Most modern motorcycles, even scooters, have disc brakes. However, this was not always the case and millions of motorcycles were built with drum brake systems. Activated by mechanical means, these systems are generally composed of 2 friction shoes pressing up against the inner wall of the drum. Simple and relatively efficient, drum brake systems possess a few inherent disadvantages. For example, when the drum becomes hot from frequent or prolonged use, it expands, the wall moving away from the shoes. Furthermore, the drum has a natural disposition to expand further on its open side, compromising full contact with the shoes. These shortcomings are further compounded by the drum brake’s poor cooling ability, a by-product of its closed design. Finally, when water or dirt enters, the centrifugal effect keeps contaminants against the wall of the drum, reducing the unit’s efficiency and increasing wear on parts.
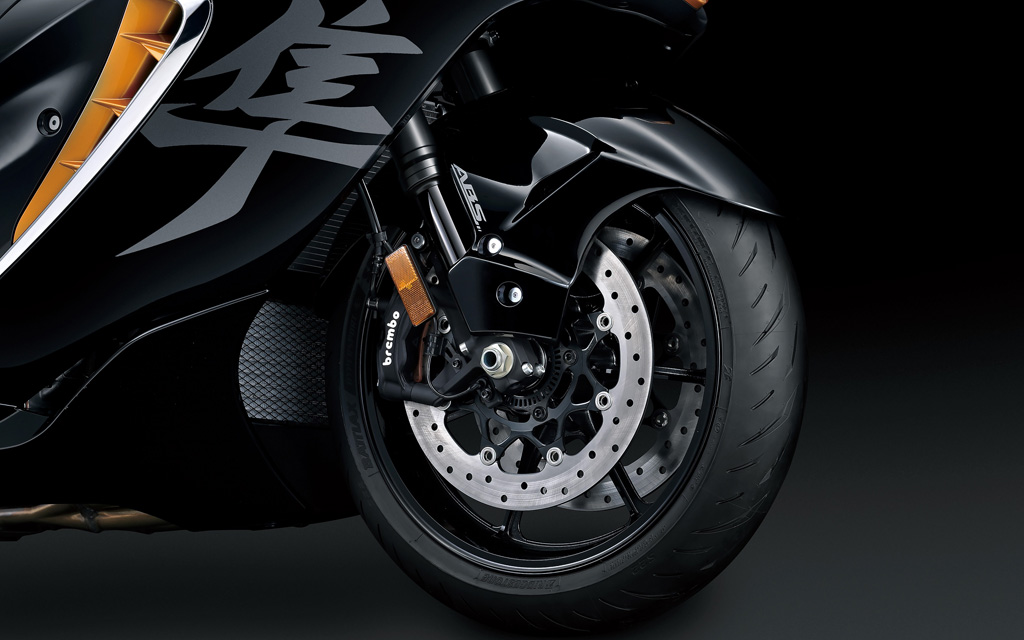
Discs
The ever-increasing performance of motorcycles, along with a growing concern with the safety aspect of riding, led Honda to introduce the 1969 Honda 750 equipped with hydraulic disc brakes front and rear. Far from being a new technology (it was patented by Briton Frederick William Lanchester in 1902), it had evolved sufficiently to be applicable on a motorcycle. At the same time, auto makers were also moving away from drums because it was easier and cheaper to build efficient and durable braking systems based on discs.
Disc systems offer many advantages, including a self-cleaning capacity, the rotational speed of the discs forcing the evacuation of impurities. Also, since both surfaces of the disc are exposed to ambient air, the cooling is superior to that of a drum. In addition, when the heat expands it, it cannot move away from the pads since they are pressed against it on both sides by the caliper.
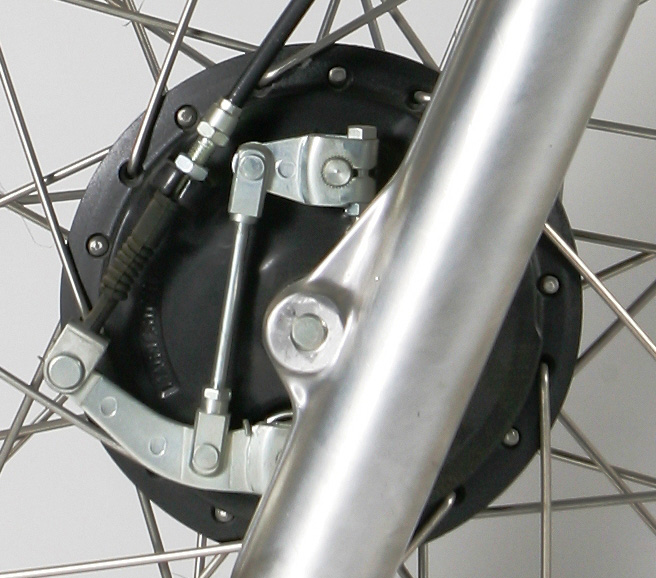
Hydraulic systems
The vast majority of modern motorcycles have hydraulic (disc) braking systems because of their superior stopping power, as well as their smooth and progressive operation. The hydraulic mechanism serves, in essence, to transport the force of your hand (or foot) to the pads. To accomplish this, the master cylinder transforms the mechanical force of our hand into hydraulic pressure. It is then carried through the line to the caliper piston, where it is converted back into mechanical force used to press the pad against the rotor.
The simplest hydraulic caliper has a single piston on one side. Known as a floating caliper (or sliding-pin) design, it uses the piston to move its adjacent pad inboard to contact the rotor. The force of the pad contacting the surface of the rotor causes the caliper to slide or float on pins, evening out pressure on both pads. The floating mechanism also allows the system to compensate for brake pad wear.
The demand for improved braking performance over the years has resulted in the more widespread use of multi-piston configurations. Opposing piston calipers can be rigidly mounted, as the pistons on both sides can move to compensate for wear.
Click here to read the part two.